Foundation Push Piers in Wichita, Sioux Falls, & Nearby
Permanent Foundation Repairs For Foundation Settlement
Do you need a permanent solution for your sinking foundation? Foundation settlement is a serious issue that requires an efficient and long-lasting repair. That is why it is crucial to schedule a foundation inspection by a professional as soon as possible to ensure the structural integrity of your home is intact.
Temperature changes cause the soil surrounding your home to expand and shrink, leading to foundation shifts over time. When foundation settlement occurs, foundations crack, and interior floors sink, leading to costly water damage, pest infestations, and other structural issues. Luckily, there are some clear indicators that you have a sinking foundation on your hands.
Signs of Foundation Settlement in Iowa, Missouri, & Nebraska
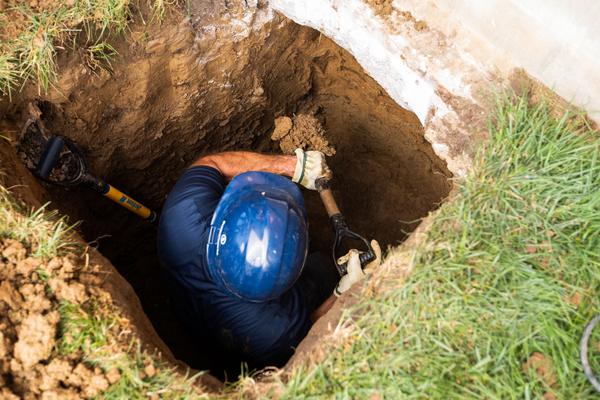
Push pier installation to repair damage caused by settling foundations in Denver, Kansas City, and nearby.
- Foundation cracks
- Wall cracks above door & window frames
- Sticking doors & windows
- Sinking or uneven floors inside the home
- A leaning chimney
Schedule a free foundation repair estimate to learn more. We proudly serve areas throughout Nebraska, Iowa, Missouri, Kansas, Illinois and Colorado. This includes the cities and towns of Wichita, Kansas City, Omaha, Denver, Springfield, Sioux City, and areas nearby.
Symptoms of a Settling Foundation
Cracks in the walls are just one of the signs you have a foundation problem on your hands. You can prevent irreparable damage to your foundation by identifying early symptoms of bowing foundation and basement walls.
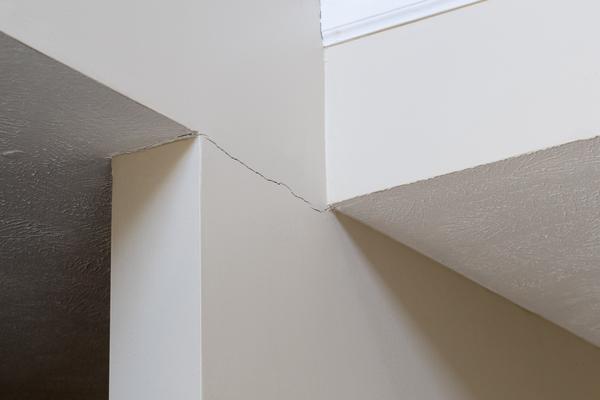
Wall Cracks
One sign of foundation settlement is cracked basement and foundation walls. Wall cracks in a failing foundation appear close to the middle in the mortar joints between blocks. These cracks occasionally form a stair-step pattern as they move up the wall.
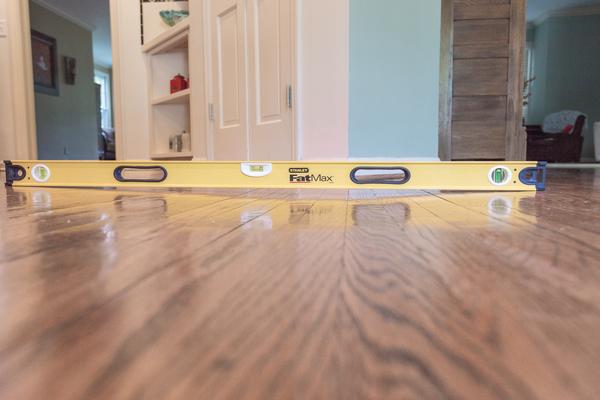
Uneven Floors
Another common symptom of foundation settlement is sinking, uneven floors inside the home. Unsure if your floors are slanted? Sections of your floor might feel bouncy, or you might have doors that are difficult to open and close. All these issues could be caused by bowing foundation and basement walls.
Fix & Prevent Foundation Settlement With Our Effective Push Piers
A secure foundation is essential for the safety and longevity of your home or business. Foundation settlement makes the entire property vulnerable, potentially resulting in expensive damages. The professionals at Thrasher Foundation Repair have the perfect solution for your foundation woes.
Features & Benefits of Supportworks Push Piers
Foundation push piers are a trusted way to stabilize your home's settling foundation. Push piers by Supportworks offer a variety of benefits; from their corrosion-resistant design to their patent-pending external sleeve, this solution will secure your foundation for a lifetime.
- 25-year warranty
- Efficient and effective installation
- Galvanized steel design
- Non-disruptive installation
- Below-grade solution
- Piers reach greater depth than alternatives
- Year-round installation
- Can lift the foundation back to its original position
When soil conditions are unknown, push piers are the least risky solution because they are driven all the way to bedrock or a stable soil layer. If you want the best opportunity to lift your home to its original position, push piers by Thrasher Foundation Repair should be your go-to option.
Schedule a Free Foundation Repair Estimate Today!
Thrasher Foundation Repair proudly provides high-quality foundation repairs and other home repair services. Backed by structural engineers and decades of experience, there is no one better equipped to complete your home improvement project. We offer highly effective solutions for foundation settlement, permanently fixing sinking floors, foundation cracks, and sticking doors and windows.
Get in touch with us to schedule a free push pier installation estimate! We proudly serve Kansas City, Omaha, Wichita, Springfield, Denver, Des Moines, Sioux City, Peoria, Fort Madison, Grand Island, and the surrounding areas.
Get a Free Estimate
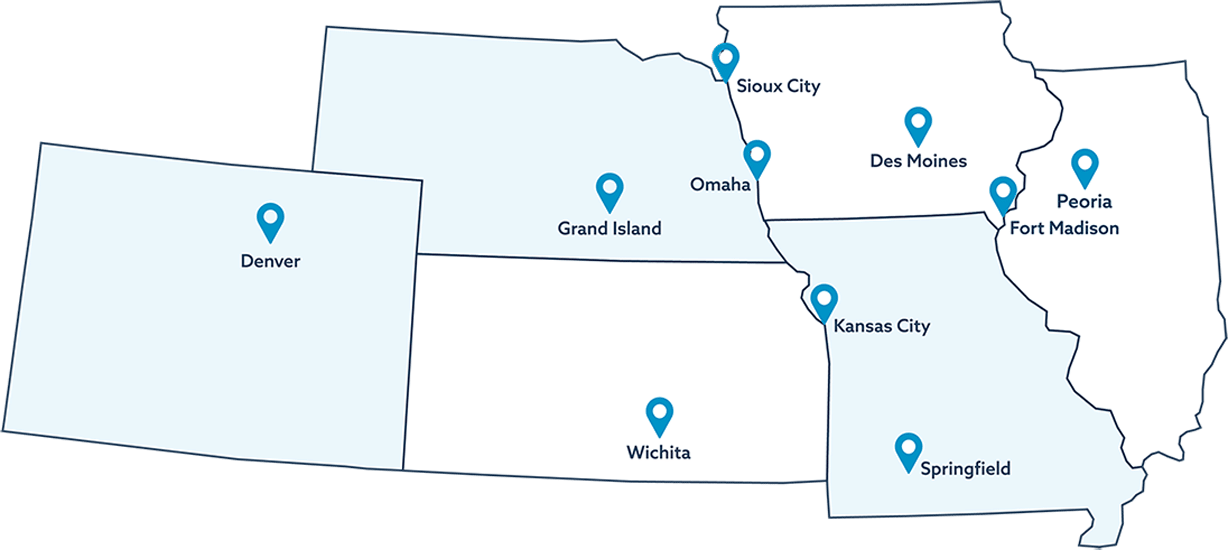
We serve the following areas
- Allenspark
- Bailey
- Black Hawk
- Breckenridge
- Cascade
- Central City
- Colorado Springs
- Como
- Conifer
- Cripple Creek
- Dillon
- Divide
- Dumont
- Eldorado Springs
- Empire
- Evergreen
- Fairplay
- Florissant
- Fountain
- Frisco
- Georgetown
- Golden
- Grant
- Green Mountain Falls
- Guffey
- Hartsel
- Idaho Springs
- Idledale
- Indian Hills
- Jamestown
- Jefferson
- Kittredge
- Lake George
- Littleton
- Louviers
- Manitou Springs
- Monument
- Morrison
- Nederland
- Palmer Lake
- Pine
- Pinecliffe
- Sedalia
- Shawnee
- Silver Plume
- Silverthorne
- Usaf Academy
- Victor
- Ward
- Woodland Park