Shane reached out to us because he noticed the basement walls were bowing in the home his grandfather built. He...
Case Studies
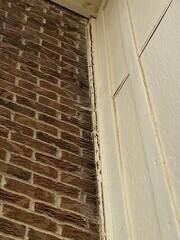
Damien, a Colorado Springs homeowner, just purchased his home and has big plans to renovate it. Before he can start...
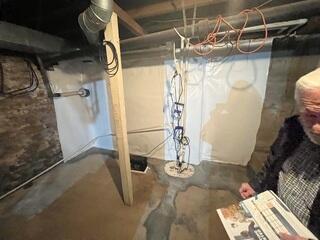
James's home in Springfield, Missouri has many waterproofing problems. The basement is constantly filling up with water, which isn't fun...
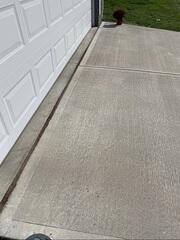
The Bennetts are currently stationed at Offutt Air Force Base and prioritize the cleanliness and upkeep of their house, always...
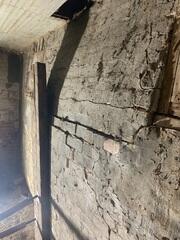
Matt and his wife have called their home, located near Grand Island, Nebraska, their own for over 30 years. However,...
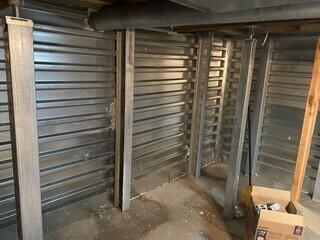
Patricia has lived in her home in Peyton, CO for quite some time now. Recently, she noticed the wall in...
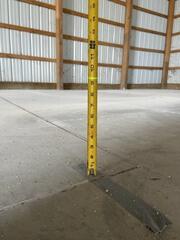
David is a farmer in Bolckow, Missouri. As a farmer, David has a lot of farming equipment, so a few...
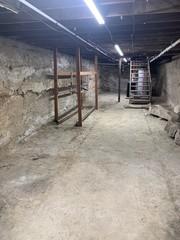
Roberta is the director at Ravenna Senior Center in Ravenna, NE. Roberta knows that the foundation of this senior center...
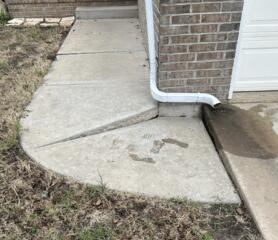
Emilio, the caring grandfather of homeowner Racine Martinez, was deeply motivated to address the foundation issues at their property due...
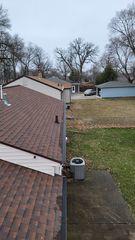
This Sioux City homeowner constantly has clogged gutters and isn't able to clean them herself. Her son drives from Des...
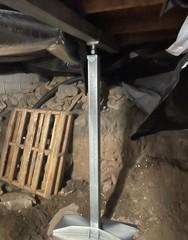
Two local homeowners in Cripple Creek, CO were concerned about the lack of support underneath the flooring system. They were...
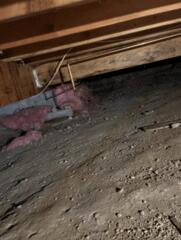
Homeownership comes with its fair share of challenges, and one of the most common issues faced by homeowners is moisture...